Distractions
I am looking at two "lost" Sundays. Lost from the standpoint of working on my E9. Last Sunday I had a bunch of things to do, culminating in a terrific concert by Debashish Bhattacharya at the Honolulu Academy of Arts. This Sunday my wife and I will be riding in the Haleiwa Metric Century Ride.
You can find more information about the ride at the Hawaii Bicycling League web site http://www.hbl.org/
Debashish is actually an old friend of mine, as is his brother Subhasis and his sister Sutapa. They have been on a U.S. tour since the beginning of April and have concerts in California and New York. More at http://www.debashishbhattacharya.com/
Wednesday, April 23, 2008
Sunday, April 13, 2008
Got Putty
Last week I was disappointed with POR Patch. I was expecting something like the old lacquer filler that came in a tube. Maybe it still does. The stuff was green, didn't run, dried fast, and sanded easily. POR Patch is a thick liquid, so thin I had a hard time filling even small holes. During the week I discovered that Red Line Automotive carries POR-15 Epoxy Putty, and stopped by after work to by a box. Inside the box are two heavy plastic bags, marked A and B. The instructions say to mix equal amounts. Sounds like what I was looking for.
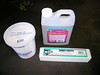
In the same photo is the tub of micro-balloons I bought to thicken POR Patch, and a bottle of POR-15 solvent. The micro-balloons are used in fiberglass work. Finding the putty may make this solution OBE, but I want to try it. I got the solvent because both times I painted with POR-15 my latex gloves leaked and I had black fingers for a week.
I must admit I was surprised to discover that the patched areas from last week were incredibly strong. I thought I would be able to push the paint right out of the small holes, but no such luck. POR-15, including the patch stuff, cures to something like phenolic. I pressed really hard with my fingernail and did not leave the slightest impression.

I decided that the best way to use the putty would be on top of a POR-15 base coat. Otherwise any rust remaining under the putty would continue to spread, weakening the foundation and eventually breaking through the surface. Maybe, maybe not. So today was about preparing a place to try the putty. I won't be able to try it until next week.

The area I chose is above the RH rear tail light. There are several small rust-throughs I thought might be suitable. To find out I had to grind away the thick layer of filler and primer that seems to be all over this car. Sure enough, what appeared was a perfect place to continue practicing the POR-15 application sequence that would provide a few places to try the putty.
After grinding away the first section of filler just above the tail-light I paused to take a picture, to show how thick the finish is. I don't thing the photo captures how much junk is on top of the sheet metal. I think the rust-throughs are an example of what happens when bondo and filler were used to repair damage. Even the best top coat is not waterproof. Eventually enough moisture can leach through the paint to reach the steel. Left untreated, it slowly starts to rust. Not so much deeper as spreading out. As I ground out the rust-through I would extend the area, exposing a thin layer of rust under the primer. I kept going, and eventually the metal under the primer was clean.

The next set of photos are after I treated the area with Metal Ready. This time I worked extra hard rinsing after using Marine-Clean, the super-detergent degreaser, but again I got bubbles what I applied Metal Ready. I hope it does not interfere with the process. I didn't bother taking a final photo; just imagine the treated area all shiny and black, and you've got it.
This time I used double gloves, and not a drop got through. But, stupid me, after everything was cleaned up I decided to get back to my shrinker tool, which meant moving the paint pot, which had drips running down the outside. So I got to test the solvent, and it works fine.
To recap, I spent about an hour grinding, ten minutes to apply Marine-Clean, fifteen minutes to rinse (a lot of trips to the sink to get clean water), a break to let it dry followed by a heat gun to finish the drying, fifteen minutes to apply Metal Ready, going around and around to keep it wet, then break for lunch. After lunch I hit it again with the dryer to ensure a bone-dry surface (rust soaks up liquids), ten minutes to paint. The trick is to clear the right amount first, and today I got it just right.
With the painting done I used the rest of my time, about an hour, tweaking the rear window patch. I finally trimmed the ends a bit. Not to final size, but enough so that I could lay the piece closer to where it will end up. It was back and forth between the shrinker and stretcher, starting with the stretcher to undo some of last week's effort. In the end I was a lot closer, but there is still a little tweaking to do. The piece still has a twist to it, which I never could control with the new tools. I got out most of it just twisting it -- it is steel, after all. I am more worried about a little arch that may have crept in. In other words, the piece is now almost perfect viewed from above, but viewed from the back the upper edge might be high compared to the ends. More next week. Maybe I'll even weld it in!
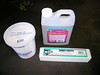
In the same photo is the tub of micro-balloons I bought to thicken POR Patch, and a bottle of POR-15 solvent. The micro-balloons are used in fiberglass work. Finding the putty may make this solution OBE, but I want to try it. I got the solvent because both times I painted with POR-15 my latex gloves leaked and I had black fingers for a week.
I must admit I was surprised to discover that the patched areas from last week were incredibly strong. I thought I would be able to push the paint right out of the small holes, but no such luck. POR-15, including the patch stuff, cures to something like phenolic. I pressed really hard with my fingernail and did not leave the slightest impression.

I decided that the best way to use the putty would be on top of a POR-15 base coat. Otherwise any rust remaining under the putty would continue to spread, weakening the foundation and eventually breaking through the surface. Maybe, maybe not. So today was about preparing a place to try the putty. I won't be able to try it until next week.

The area I chose is above the RH rear tail light. There are several small rust-throughs I thought might be suitable. To find out I had to grind away the thick layer of filler and primer that seems to be all over this car. Sure enough, what appeared was a perfect place to continue practicing the POR-15 application sequence that would provide a few places to try the putty.
After grinding away the first section of filler just above the tail-light I paused to take a picture, to show how thick the finish is. I don't thing the photo captures how much junk is on top of the sheet metal. I think the rust-throughs are an example of what happens when bondo and filler were used to repair damage. Even the best top coat is not waterproof. Eventually enough moisture can leach through the paint to reach the steel. Left untreated, it slowly starts to rust. Not so much deeper as spreading out. As I ground out the rust-through I would extend the area, exposing a thin layer of rust under the primer. I kept going, and eventually the metal under the primer was clean.

The next set of photos are after I treated the area with Metal Ready. This time I worked extra hard rinsing after using Marine-Clean, the super-detergent degreaser, but again I got bubbles what I applied Metal Ready. I hope it does not interfere with the process. I didn't bother taking a final photo; just imagine the treated area all shiny and black, and you've got it.


This time I used double gloves, and not a drop got through. But, stupid me, after everything was cleaned up I decided to get back to my shrinker tool, which meant moving the paint pot, which had drips running down the outside. So I got to test the solvent, and it works fine.
To recap, I spent about an hour grinding, ten minutes to apply Marine-Clean, fifteen minutes to rinse (a lot of trips to the sink to get clean water), a break to let it dry followed by a heat gun to finish the drying, fifteen minutes to apply Metal Ready, going around and around to keep it wet, then break for lunch. After lunch I hit it again with the dryer to ensure a bone-dry surface (rust soaks up liquids), ten minutes to paint. The trick is to clear the right amount first, and today I got it just right.
With the painting done I used the rest of my time, about an hour, tweaking the rear window patch. I finally trimmed the ends a bit. Not to final size, but enough so that I could lay the piece closer to where it will end up. It was back and forth between the shrinker and stretcher, starting with the stretcher to undo some of last week's effort. In the end I was a lot closer, but there is still a little tweaking to do. The piece still has a twist to it, which I never could control with the new tools. I got out most of it just twisting it -- it is steel, after all. I am more worried about a little arch that may have crept in. In other words, the piece is now almost perfect viewed from above, but viewed from the back the upper edge might be high compared to the ends. More next week. Maybe I'll even weld it in!


Sunday, April 6, 2008
The Shrinker Finally Arrived
Talk about a slow boat to China. Well, from China to the mainland and then back to Hawaii. It was mid-February when I ordered a metal shrinker and stretcher set from Harbor Freight. To be fair they did quote 4-6 weeks shipping to Hawaii because to hold down the cost it had to go by sea. Sure seems longer than that. Like six months. Time does not always fly.
When the box arrived at home I opened it up and was not pleased by what I found. The inside was full of styrofoam bits. It looked as though mice had moved in. Nuts and washers were rattling around inside because the platic bag of hardware had a big hole in it. I gathered up what I could find and put it in a zip lock. Today at the shop the first thing I did was to take everything out and clean it up.
There was more unhappiness. Lots ot dings and scratches. The paint on the bottom of both tools was worn off as if they had been used. Was this a demo? A return? I was starting to have bad thoughts about Harbor Freight. Then it occured to me that all of the wear could be explained by the condition of the styrofoam packing. These tools are unusually heavy. They traveled thousands of miles rubbing against each other due to inadequate packaging. No wonder they don't look fresh.

There was already a hole in the bench near my car so I bolted down the shrinker and experimented with some scrap. My first attempt was with the same steel I was making patches with. When I pushed down the lever nothing happened. I was worried it was too thick. Great, I'll have to buy thinner stock and start over with the rear window patch. Aluminum was a snap. Then I tried inserting the steel part way, and that worked. I had to push down pretty hard, but it worked.
With that worked out I start to practice on the end of the rear window patch I had previously messed up -- the hammering I had done on the left side resulted in the patch bending the wrong direction. Immediately the end started bending the way I anticipated, but I could not be sure how that would affect the end result. I needed to shrink both edges to get the whole thing to arch the right way, so I flipped the piece around and worked on the opposite side. Sure enough, the piece began to arch, just as I had hoped it would, only way too much.
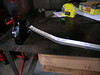
Now I know why Harbor Freight seemed so intent on selling the shrinker and the stretcher as a set. I mounted the stretcher and experimented undoing some of the shrinking I had done, and it worked perfectly.
Inspired, I went back to the shrinker and went to work on the whole piece. Applying what (little) I had learned, I did not press so hard and I advanced the work a little farther between presses. Even then, when I was done with the second side I had too much curve. I was a also out of time, so I left the stretcher tweaking for next time. Despite overshooting the curve I came away feeling really good about this progress, the first time I had felt that good in a long time.

Last week I expressed my disappointment with POR-15 as a filler for small holes, and with leaky Latex gloves. During the week I checked their web site to see if I needed a different type of glove (nope, they sell Latex) and while looking for the answer I stumbled across this: POR-15 Putty really is a slightly thicker POR-15 paint, in a tube. They also sell a filler, and its description sounds like what I expected putty to be. I don't remember seeing it at Redline Automotive, but I'll check tomorrow.
One thing I did buy during the week was a canister of fiberglass microballons, which are intended to be used in fiberglass construction to build up fairings. I was going to experiment with it as a POR-15 thickening agent today but the arrival of the shrinker kind of took precedence. Besides, it was a wet, rainy day, not the best for paint that sets from moisture in the air.
Last week I tried building up a fill on a larger sized small hole by covering the hole with masking tape and painting from behind. It sort of worked. Well, on the POR-15 web site they describe the same technique, only they suggest putting the tape on the back side. Interesting.
One thing that is killing me is the week-long delay between sessions. So, when the instructions say to wait four hours before applying a second coat, I'm out. Back when I was building radio-controlled sailplanes I used a lot of cyanoacrylate glue. As fast as it was drying, there were times when an extra kick was a real help, and for that I used a spay-on activator. Maybe if I sprayed some water on POR-15 I could create the same effect? I could sure get a lot more done in a day.
Finally, the guy with a nice '76 Corvette was back today in the stall next to mine. His name is Derrick. I took a couple of pictures on his car, just for the heck of it.
When the box arrived at home I opened it up and was not pleased by what I found. The inside was full of styrofoam bits. It looked as though mice had moved in. Nuts and washers were rattling around inside because the platic bag of hardware had a big hole in it. I gathered up what I could find and put it in a zip lock. Today at the shop the first thing I did was to take everything out and clean it up.


There was more unhappiness. Lots ot dings and scratches. The paint on the bottom of both tools was worn off as if they had been used. Was this a demo? A return? I was starting to have bad thoughts about Harbor Freight. Then it occured to me that all of the wear could be explained by the condition of the styrofoam packing. These tools are unusually heavy. They traveled thousands of miles rubbing against each other due to inadequate packaging. No wonder they don't look fresh.


There was already a hole in the bench near my car so I bolted down the shrinker and experimented with some scrap. My first attempt was with the same steel I was making patches with. When I pushed down the lever nothing happened. I was worried it was too thick. Great, I'll have to buy thinner stock and start over with the rear window patch. Aluminum was a snap. Then I tried inserting the steel part way, and that worked. I had to push down pretty hard, but it worked.
With that worked out I start to practice on the end of the rear window patch I had previously messed up -- the hammering I had done on the left side resulted in the patch bending the wrong direction. Immediately the end started bending the way I anticipated, but I could not be sure how that would affect the end result. I needed to shrink both edges to get the whole thing to arch the right way, so I flipped the piece around and worked on the opposite side. Sure enough, the piece began to arch, just as I had hoped it would, only way too much.
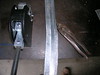
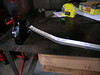
Now I know why Harbor Freight seemed so intent on selling the shrinker and the stretcher as a set. I mounted the stretcher and experimented undoing some of the shrinking I had done, and it worked perfectly.
Inspired, I went back to the shrinker and went to work on the whole piece. Applying what (little) I had learned, I did not press so hard and I advanced the work a little farther between presses. Even then, when I was done with the second side I had too much curve. I was a also out of time, so I left the stretcher tweaking for next time. Despite overshooting the curve I came away feeling really good about this progress, the first time I had felt that good in a long time.



Last week I expressed my disappointment with POR-15 as a filler for small holes, and with leaky Latex gloves. During the week I checked their web site to see if I needed a different type of glove (nope, they sell Latex) and while looking for the answer I stumbled across this: POR-15 Putty really is a slightly thicker POR-15 paint, in a tube. They also sell a filler, and its description sounds like what I expected putty to be. I don't remember seeing it at Redline Automotive, but I'll check tomorrow.
One thing I did buy during the week was a canister of fiberglass microballons, which are intended to be used in fiberglass construction to build up fairings. I was going to experiment with it as a POR-15 thickening agent today but the arrival of the shrinker kind of took precedence. Besides, it was a wet, rainy day, not the best for paint that sets from moisture in the air.
Last week I tried building up a fill on a larger sized small hole by covering the hole with masking tape and painting from behind. It sort of worked. Well, on the POR-15 web site they describe the same technique, only they suggest putting the tape on the back side. Interesting.
One thing that is killing me is the week-long delay between sessions. So, when the instructions say to wait four hours before applying a second coat, I'm out. Back when I was building radio-controlled sailplanes I used a lot of cyanoacrylate glue. As fast as it was drying, there were times when an extra kick was a real help, and for that I used a spay-on activator. Maybe if I sprayed some water on POR-15 I could create the same effect? I could sure get a lot more done in a day.
Finally, the guy with a nice '76 Corvette was back today in the stall next to mine. His name is Derrick. I took a couple of pictures on his car, just for the heck of it.


Subscribe to:
Posts (Atom)