Today I decided to take the Lotus. Usually I take my big old Dodge Carvan, which is full of stuff I can't leave at the shop, like paints and lubricants. Today I would't need any of that, so I took the opportunity to enjoy the Lotus.
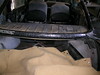
The day started with an inspection of last week's welds. I spotted several places where the bond at the bottom was unconvincing, so I started there. While I was doing that I ran a little bead along each of the three joints, to prevent them from flexing relative to each other. Next I ground down everything -- I could leave a lot because the epoxy filler will cover it -- and pushed hard against each segment, to check the top weld. I found four in a row near the center than had not stuck. A little more welding, testing, more welding, until finally everything was solid.
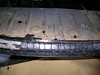
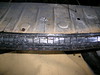
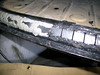
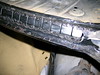
While I did the last pass of grinding I ran the wheel over the bare metal to give the filler a rough surface to hold onto. On when the latex gloves and on went the POR-15 epoxy filler. I always cut each part about 1/8 in. thick, because that makes a batch just the right size to put on before it starts to kick off. I went through maybe half a dozen of these batches.
I pushed hard to force the filler into the cracks and gaps, my thinking being that this stuff is somewhat structural and will help tie all the little pieces together. If the pieces move relative to each other the finish coat will crack.
When I had all the new parts done I still had some time left, so I filled in the places I had left uncovered on the first (left-most) patch. Next week I can get right to work shaping the entire piece.
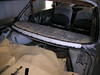
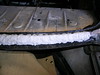
On my way home I stopped for gas. The Lotus fuel gage was reading beyond full, which meant it was getting low. When I made new tanks the sending unit ended up wired backwards, and physically the float cannot swing all the way up or down, so the gage reads empty when the tank is 7/8 full and full when it's 7/8 empty. The gage sits right in front of the passenger, and makes for interesting conversation. Anyway, to fill up cost $40. That's right. Slightly less than nine gallons, $40. Well, it is a Lotus. It's worth it.
Then came the embarrassment of the engine not starting. It never cranks enthusiastically, especially when it's hot. This was one of those times. Then it stopped cranking altogether. What happened next is why I buy my gas at Kahala Shell and not Costco or 7-11. One of the attendants brought out a jumper battery -- without my asking! -- and helped me get it going. No charge. I really do have to replace that lousy positive cable. Hats off to Kahala Shell.