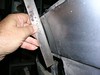
The first thing to do was to put some curve in the new patch. It fits inside a panel with a concave curve, the one I have been having trouble sanding, and without at least an approximation the fit at the top and bottom would be way off. A little work with a hammer and shot bag took care of that.

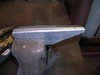
Now that the top went where it was supposed to it needed to fit better up against the underside. To achieve that I needed to trim away some of the top on the inboard end.
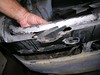
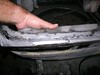
As usual it meant rough cutting with the dia grinder and a seemingly endless cycle of grind, file and fit, with walking back and forth from the workbench to the car. I should have invested in a portable workbench, except the one I use has a heavy steel top. Hard to beat.

When the fit was good it was time to prepare the host sheet metal for welding. Since the patch goes inside a doubler I cannot weld from the inside, so I had to drill holes in the original panel. This means more work grinding and smoothing, but it can't be helped.

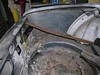
Because of its location there is no obvious way to hold it in place while welding. The solution turned out to be a long iron bar that just fits through one of the holes in the doubler and presses against the folded edge of the patch.
At this point I was too tired to weld. The way I felt, if I tried to weld I would just make a mess and end up having to do it all over again. So, I doused everything with MetalPrep and called it a day.
No comments:
Post a Comment