Yesterday I picked up new front wheel bearings and retaining rings, $140 at NAPA. The hard part of the job sounded like pressing out the old bearings, but the shop has an excellent hydraulic press. When I removed the wheel I noticed that it was not just worn, some of the steel belt was starting to show through. Carl, the shop manager, expressed some doubt that my problem was with the bearings and suggested I go far enough with the RH side to where we could get a good feel without removing the hub.


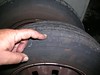
With the caliper out of the way, the disk off, and the hub removed from the driveshaft it was possible to check the bearing and it was perfect. No sign of the 125,000 miles on it. Obviously not the source of problem. As I was putting everything back I discovered what turned out to be the problem, worn tie rod end bearings. The LH side was fine; nice and tight. Not only was the RH side loose, when I rocked the hub side to side it made the same sound I was getting on the road. NAPA had the parts in stock, so I put the car back down, grabbed some lunch, whizzed back to Kaimuki and exchanged the bearings for the LH inner and outer tie rod bearings. The good folks at Larry's even gave me $50 back, in cash!
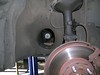

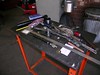
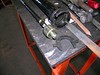
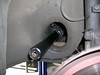
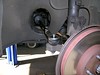
I actually hate being in situations like this. I had four hours to do a job I have never done before on the only usable car in the family, and the shop is closed on Monday and Tuesday. Do or die. It does help in getting things done.
Right off the bat I hit a snag. The inner end of the steering rack boot is held on by a one-time steel band. It has to be cut off without tearing the boot. Not enough room for long handled cutters, not enough leverage from my short handled dikes. (Did you know that dikes is a portmanteau of "Diagonal CutterS?" Thank you Wikipedia.) I spent an excruciatingly long time on this.
Before removing the outer rod end bearing I counted the number of exposed threads. With the rod end and boot removed I could see where the lock washer was bent over the two flats on the inner bearing retainer, but getting to them to straighten them out seemed impossible. Luckily I found a funny shaped punch that fit perfectly.
There was no way to get an open end wrench on the retainer. Hardly enough room for a crow's foot wrench, and none that big available. Luck for me the shop has a nifty tie rod tool that made the job a piece of cake.
On the bench I reassembled the old rod end so that there was the same numbered of grooves showing, measured 15 1/8 in. exactly, assembled the new set, and counted the grooves. This was where it needed to be back on the car.
There were no snags after that. I used a long tie wrap to secure the boot. The car now drives smooth, tight, and quiet. I do need to replace that tire.