The flange that the window sits on consists of two or three layers of sheetmetal spot welded together. Along the right vertical joint (the C-pillar) the gap is filled with lead, but along the bottom and left side there are many gaps.
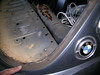


The first task was to remove the old paint and what little loose rust was present. For this I used a die grinder and at first a synthetic wire wheel followed by a real wire wheel. After blowing all the dust away I washed the area with Marine-Clean, and when that was dry I brushed on a coat of Metal-Ready. The instructions said to keep the area wet for fifteen minutes so I kept going around and around.
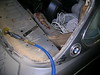

Up to this point everything worked fine, but here is where I ran into the problem I was concerned about. I gave the Metal-Ready coat an hour to dry, and after an hour it was still tacky. I had to call it a day without applying any POR-15.
The shop is closed Mondays and Tuesdays, so it will be Wednesday before I can even attempt to apply a coat of POR-15. This area deserves two coats, which means going again on Thursday.
Painting projects are difficult for this reason, especially when you only have one day a week to work on them. Surface prep takes a long time, and waiting for something to dry chews up big chunks of valuable time. maybe a hair dryer would help.
Update: Pics to show how POR-15 turned out. First two show zinc (white splotches) where Metal-Ready converted rust, before applying POR-15. The rest show treated area. POR-15 brushed on easily.
This job used no more than half of the very small can of POR-15 that came in the starter kit. I poured it out into a clean soup can. After I was done I did not bother to clean up, just tossed the tin can and brush.
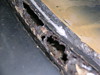

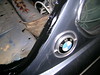
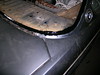

